Screen printing technology
A) 4 structures of screen printer:
1) Worktable. To put fixture and article, different type of screen printer with different worktable, there are mainly 4 styles worktable: flat worktable, T type worktable, vacuum worktable and cylinder worktable. The size of worktable can be customized according to the article.
2) Screen printing system. Install squeegee to scrape ink.
3) Screen plate system. To put screen plate and ink.
4) Control panel. There are 2 kinds of printing model, one time printing for sample test and automatic printing for mass production.
B) 4 kinds of screen printing machine:
1) According to printing model:manual screen printer, pneumatic screen printer and electric screen printer。
2) According to print color: single color screen printer,2 colors s printer, 4 colors screen printer, 6 colors screen printer, 8 colors screen printer and 10 colors screen printer.
3) According to the worktable system: vacuum flat screen printer (suit to print soft and thin article, as paper, film), T type worktable screen printer (suit to print hard plane product), cylinder screen printer(suit to print round and ellipsoid product, as bottle), and rotate screen printer( spider machine suit to print on garment, bag etc)
4) According to the print colour:flat screen printer and cylinder screen printer.
C) 4 factors about screen printing:
1) Screen plate. Take net yarn tension, mesh count, screen frame size into consideration to make it according the material of article.
2) Squeegee.
3) Screen printing ink. There are solvent ink, UV ink and varnish. You should choose ink according by the material of article to test.
4) Fixture. Make jig by the shape and size of article. General request is that the top of cross section of jig parallel to the screen plate.
D) How to choose squeegee?
1) Mixed type squeegee suit high speed screen printing, because the side touch the product in front of squeegee can cure.
2) Round type squeegee use for plane article, like paper, garment, etc, especially good for thick and thin lines printing and dot matrix printing.
3) Triangle sharp type squeegee can print on glass and plastic bottles, also with textile fine printing.
4) Groove squeegee for container such irregular product printing.
5) By the shape of product. Rectangular section for plane article, triangular section for cylinder article,
6) By the hardness of product: 55—65 degree is soft style, for medium press regular and irregular article, 65—75 degree is medium style, for all kinds of printing, 75—95 degree is hard style, for fine screen printing.
E)5 features of good screen printing ink:
(1)Well viscosity to the print surface.
(2)good liquidity.
(3)usually standard ink thickness is 7μm。
(4)ink gloss without change by the article surface.
(5)Dry fast, and not effect ink viscosity.
F) How to control the thickness of screen ink?
-
1)
Ink printed on article is thicker if the angle of squeegee is smaller, and the opposite also works.
-
2)
Ink is thinner if the viscosity of ink is bigger and thicker, and the opposite also works.
-
3)Ink is thicker if the substrates of article are coarser.
-
4) Ink is thinner if print speed is higher, it works the opposite side.
-
5) Ink gets thicker if the print environment with higher temperature.
G)Fixture
Fixture is specially made by the shape and size of product, clip product on worktable steady, now days it’s very popular to make jig by putty and hardner.
Cylinder screen printer should make one set of fixture including gear.
Screen plate making process:
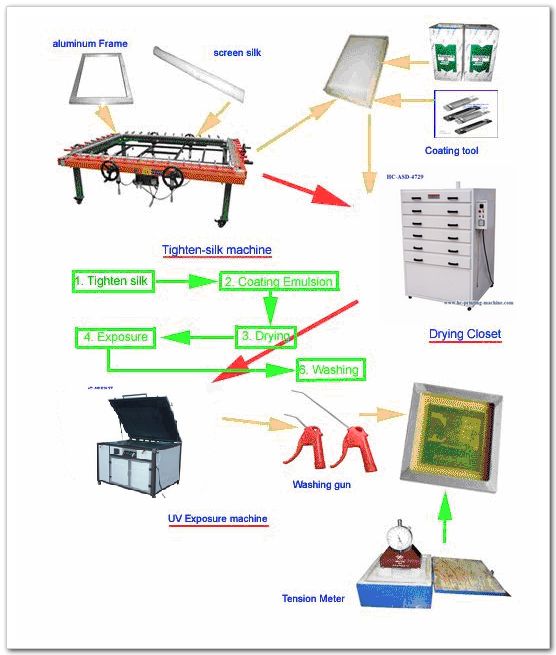
Pad printing machine technology
A) 6 structures of pad printer:
1) Worktable. To put fixture and article, different type of pad printer with different worktable, there are mainly 4 style worktable: basic, shuttle, conveyor, disc one. The size of worktable can be customized according to the article.
2) Pad printing system.
3) Supply ink system. Open ink tray and ink cup one.
4) Scrape ink system. Ink cup system accomplishes cover ink and scrapes ink at the time, while open ink tray use doctor blade to scrape ink.
5) Control panel. There are 2 kinds of printing model, one time printing for sample test and automatic printing for mass production.
6) Ink. Solvent pad printing ink, screen printing ink and UV pad printing ink for open ink tray pad printer; usually solvent pad printing ink and screen printing ink for ink cup pad printer.
B) 5 kinds of pad printer:
1) According to printing model:manual pad printer, pneumatic pad printer and electric pad printer.
2) According to ink supply system:open ink tray pad printer and ink cup pad printer, the last one save more ink and protect environment.
3) According to print color: single colour pad printer,2 colours pad printer, 4 colors pad printer, 6 colors pad printer, 10 colors pad printer.
4) According to the worktable system: shuttle pad printer, conveyer pad printer and automatic conveyer pad printer.
5) According to the print article:flat pad printer and cylinder pad printer.
C) 4 factors about pad printing:
1) Rubber Pad
2) Plate. 3 kinds of plates are thick steel plate, thin steel plate and resin plate.
3) Pad printing ink. There are solvent ink and UV ink. You should choose ink according by the material of article, test and decide.
4) Fixture. Make jig by the shape and size of article.
5) Doctor blade.
D) How to choose pad?
1) Better to choose round or square pad if product suit.
2) If product under pressure, you’d better choose hard pad, because hard one with longer life.
3) Usually the diameter of pad is 3mm bigger than print size.
4) If print design with lots of hair line, soft pad is better.
5) Soft pad is better for uneven surface of article than hard pad.
6) The pressure depth between pad and article no more than 1/3 height of pad, or pad will be damaged easily, and designs will deformation fuzzy.
E) How to maintain pad?
1) Put pad in 5—25℃ dry and ventilated condition.
2) Please wash the new pad by alcohol before use before it got a mold release.
3) Pad may be attached dustiness when printing, please use Tina solvent clean it, to keep it clean and dry.
F) Nice steps to make pad plate:
1、Output film. According to the digital artworks provided by the customer, the films are output by an image setter Laser output machine. Most of films for pad printing process is positive.
2、Clean the pad plate by Tina solvent to wipe off greasy dirt.
3、Cost emulsion. Drop some Fuji emulsion on the surface of pad plate, put it in the emulsion coater rotate ensure emulsion cover on the plate evenly.
4、Dry. Put the plate which with emulsion to the drying closet for 10-15minutes, temperature is 120-150℃.
5、Exposure. Cover film on plate, then put them on the UV exposure machine, set up the time to expose 30-60 seconds; the emulsion side should close to the glass of exposure unit.
6、Develop. Drop a few Fuji developers about 10 seconds, clean the plate by water when there is image appear the plate. And dry plate by dryer at the temperature of 40-50℃.
7、Cover the non etching area by Scotch tape.
8、Etching. Use brush dip some etching liquid brush on the image size evenly. After 40 to 100 seconds there is a clean image.
9、Cleaning. Wash the etching liquid by clean water; rip out the tape, clean the left emulsion by Tina solvent.
If precision printing is required, please measure the depth of plate, standard depth should be 19-23UM.
G) 5 features of good pad printing ink:
(1)Well viscosity to the print surface.
(2)good liquidity.
(3)usually standard ink thickness is 7μm。
(4)ink gloss without change by the article surface.
(5)Dry fast, and not effect ink viscosity.
H) Doctor blade
Please note the following 3 tips when choose doctor blade:
1) Usually use 0.25mm thickness and good elasticity straight doctor blade.
2) Blade should be sharp without damage.
3) There must be some angle between doctor blade and pad plate.
I)Fixture
Fixture is specially made by the shape and size of product, clip product on worktable steady, now days it’s very popular to make jig by putty and hardner.
Pad plate making process:
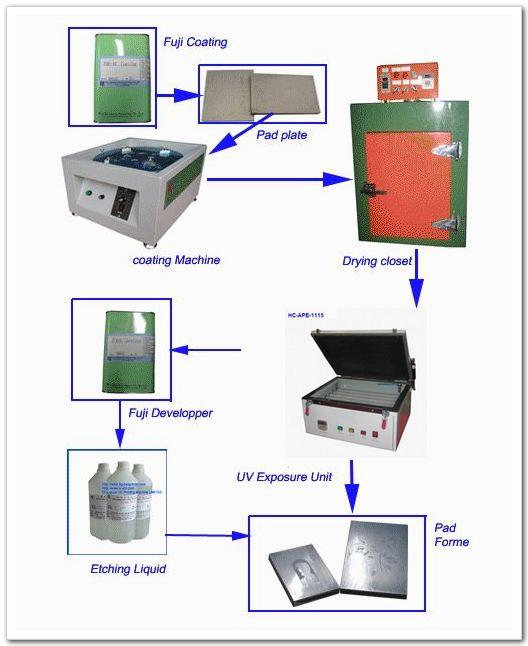
Hot stamping machine technical support
A) Hot stamping machine structure:
1) Worktable. To install fixture and article, there are mainly 2 kinds of worktable, flat worktable and shuttle worktable hot foil stamping machine.
2) Stamping system. Stamping head with hot plate inside, hot plate can stamp up and down.
3) Foil feed system. Install hot foil and heat transfer film, it was controlled automatically.
4) Control system. Ensure printing process automatically and stably. Control panel has 2 kinds of printing mode, single printing for sample test and automatic printing for mass production.
B) 4 Print factors for hot stamping machine:
1) Hot plate. There are silicon rubber plate, copper plate and zinc plate. They are fixed to the hot plate by high temperature tape or high temperature glue.
2) Hot foil. It must be test before mass production according to the material of article.
3) Temperature and pressure.
4) Fixture. It must withstand greater pressure and high temperature.
C) Different type of hot foil stamping machine:
1) Plane hot stamp machine. It’s for plane product printing.
2) Cylinder hot stamping machine, it’s for cylinder and cone product.
3) Plane and cylinder hot stamp machine, it can print on both plane and cylinder product.
D) 4 factors to effect stamp print effect:
1) Pressure
2) Temperature
3) Hot foil
4) Hot stamp plate
E)How to fix stamp plate?
1) By high temperature tape: Cut a piece of high temperature tape, size is the same as stamp plate, stick it to the back of stamp plate, then put it on the worktable, heating the hot stamping machine to 100-200 degree, then start the machine printing, so heat plate push down on the stamp plate, after heat plate rise up, the stamp plate and heat plate already stick together closely.
2) by high temperature glue: Apply glue evenly all over both stamping plate side and stamping former plate side, wait for 10-15 minutes, then assemble the two sides and press for a minutes.
Hot stamp forme
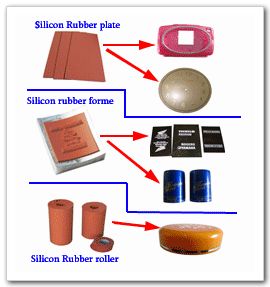
Heat press machine technology
1)By the function, there are flat heat press ( for t shirt, garment and cloth), mug heat press ( for cylinder article, like cup, mug), cap heat press and plate heat press. 2)By power operation, there are 3 types, manual heat press, semi automatic heat press and fully automatic heat press. 3)By structure, common heat transfer machine, high pressure heat press, swing heat press, pneumatic and hydraulic heat press. B) Heat press theory: Though pressure and temperature, after some time the hot plate will transfer image from heat transfer paper or heat transfer ink to article. Heat transfer paper use inkjet printer output the image, then transfer to garment by heat press machine. There are mainly 2 kinds of heat transfer paper, light colour paper for light colour garment and dark colour paper for dark colour clohthing. D) Sublimation description: 1) Inputting digital photos to computer by digital camera or scanner. 2) Edit photos with Image Processing software to make the specifications compatible with the pressing objects. 3) Print images by ink-jet printer onto ink-jet paper or heat transfer paper, please use sublimation ink to do this. 4) Transfer the images onto article by using a proper heat transfer machine. Sublimation process: 
|
|
t Paragraph Content